Defeating the Ravages of Corrosion: How to Stop Saltwater and Freshwater Corrosion
Corrosion poses a significant threat to metal surfaces in saltwater and freshwater environments, leading to safety concerns, reduced lifespan, and increased costs. Understanding the causes and implementing effective preventive measures are crucial to combat this pervasive issue. In this article, we will explore the causes of corrosion, along with practical strategies and maintenance practices to stop corrosion caused by saltwater or freshwater. By taking proactive steps, we can protect valuable metal assets, ensure longevity, and enhance operational efficiency.
Understanding the Causes of Corrosion
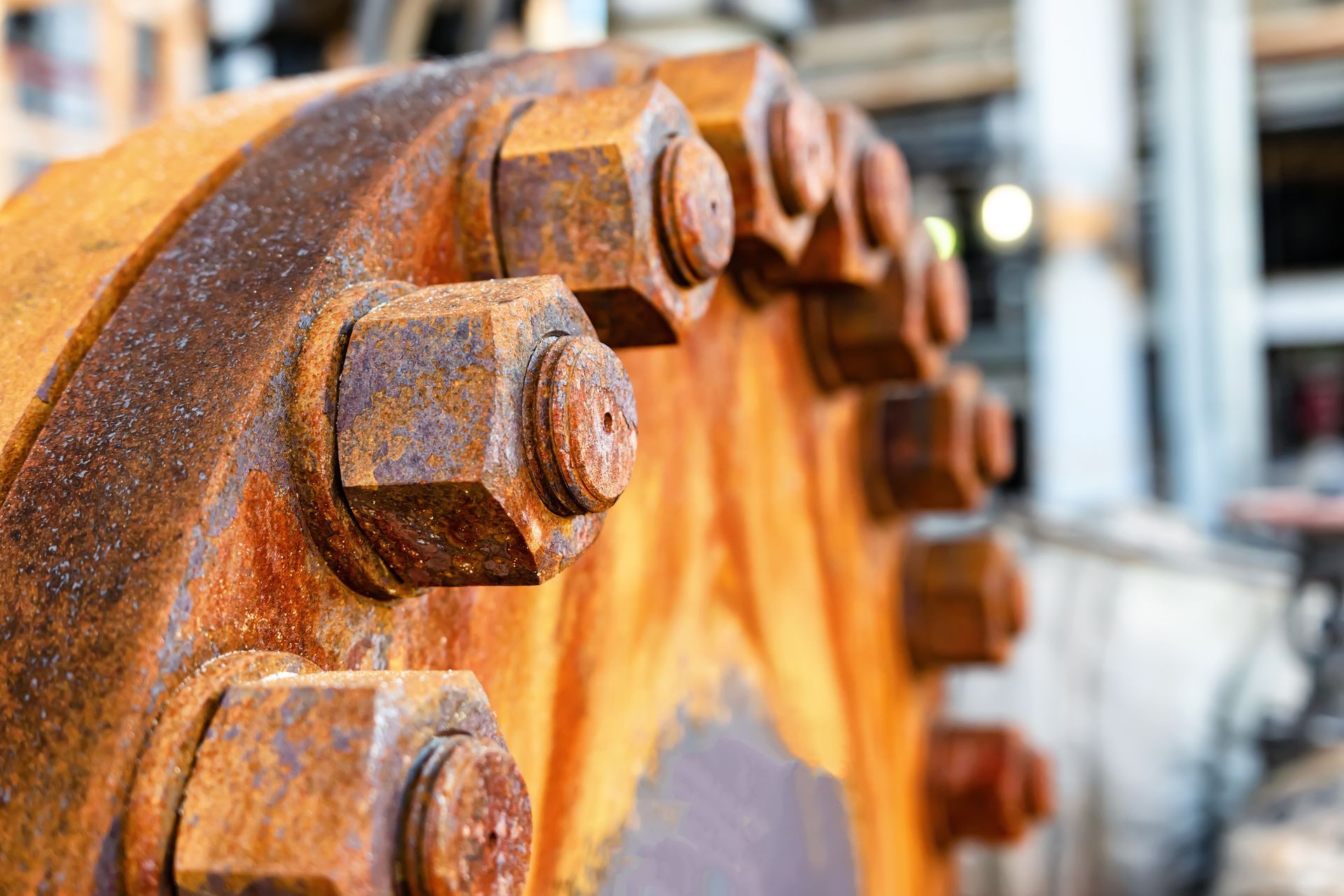
Corrosion is
a natural process that occurs when metal reacts with its surrounding environment. Several factors contribute to the causes of corrosion, including:
- Moisture: The presence of water or moisture is a primary catalyst for corrosion. It provides the necessary medium for electrochemical reactions to occur, allowing ions and electrons to transfer between the metal surface and the environment.
- Oxygen: Oxygen plays a vital role in most corrosion processes. It combines with metal atoms to form metal oxides or hydroxides, weakening the metal's structure and causing degradation.
- Electrolytes: Corrosive environments often contain electrolytes, such as salts or acids, which increase the conductivity of the surrounding solution. Electrolytes facilitate the flow of ions, accelerating the electrochemical reactions that lead to corrosion.
- pH Level: The pH level of the environment influences the corrosion rate. Highly acidic or alkaline conditions can be corrosive to certain metals, causing accelerated degradation.
- Temperature: Elevated temperatures can accelerate corrosion processes by increasing the rate of chemical reactions. Thermal fluctuations, such as thermal cycling or exposure to extreme heat, can also contribute to corrosion.
- Chemical Exposure: Exposure to chemicals, such as acids, salts, or industrial pollutants, can intensify corrosion processes. Certain chemicals can directly attack the metal surface, initiating or accelerating corrosion.
- Galvanic Corrosion: When dissimilar metals come into contact in the presence of an electrolyte, galvanic corrosion can occur. This type of corrosion happens due to the electrochemical potential difference between the metals, leading to the more reactive metal corroding while the less reactive metal remains protected.
It's important to note that the specific
corrosion mechanisms and rates can vary depending on the type of metal, the environment, and other factors. Understanding the causes of corrosion is essential for implementing preventive measures and selecting appropriate protective coatings to mitigate or minimize the effects of corrosion.
Preventative Measures
For atmospheric corrosion, such as rust from exposure to weather or water, one effective approach is to apply protective coatings of zinc, aluminum, or zinc and aluminum blends to exposed surfaces. These materials not only shield vulnerable areas but also provide galvanic protection to the underlying steel. By employing this method, one can safeguard against the detrimental effects of corrosion while preserving the integrity of the steel substrate. Aluminum coatings, in particular, will form a hard, protective aluminum oxide “shell” that provides both sealing of any connected porosity and mechanical wear resistance.
Thermal spraying, also known as metalizing, offers a highly effective preventive method for corrosion in various industries. By depositing a protective coating onto metal surfaces, thermal spray coatings act as a barrier against corrosive agents, such as saltwater or chemicals. The versatility of thermal spray allows for the application of corrosion-resistant materials, including metals, alloys, ceramics, and polymers, tailored to specific environmental conditions. These coatings provide enhanced durability, excellent adhesion, and superior resistance to wear, corrosion, and erosion. With its ability to create uniform, dense, and well-bonded coatings, thermal spray effectively safeguards metal components, extends their service life, and minimizes the risk of corrosion-related damage. Additionally, thermal spray coatings can be customized in terms of thickness, composition, and surface texture, allowing for tailored corrosion protection solutions.
Overall, thermal spray proves to be a reliable and versatile preventive method, offering long-lasting corrosion resistance and ensuring the integrity and reliability of metal assets in diverse industrial environments.
- Preventive Measures for Saltwater Environments
In saltwater environments, selecting corrosion-resistant materials is crucial to stop saltwater corrosion on metal. Implementing protective coatings, such as galvanization, metallizing, or anodizing, adds an extra layer of defense. Sacrificial anode systems and cathodic protection methods can also be employed to prevent corrosion. Regular maintenance and inspection practices play a vital role in early detection and addressing corrosion concerns. - Preventive Measures for Freshwater Environments
Corrosion in freshwater environments presents unique challenges. Utilizing protective coatings tailored to freshwater conditions helps safeguard metal surfaces. Corrosion inhibitors and passivation techniques can be applied to mitigate corrosion risks. Proper design and installation practices that minimize contact between metal surfaces and water are essential. - Maintenance and Inspection Practices
To combat corrosion, regular cleaning and removal of debris are crucial in preventing accelerated corrosion. Implementing a routine inspection schedule allows for the timely identification of corrosion signs. Prompt repair of damaged coatings or corroded areas is essential, as is monitoring and maintaining cathodic protection systems, if applicable. - Education and Training
Education and training play a significant role in combating corrosion. Educating personnel about corrosion prevention and control helps foster a proactive approach. Proper training on handling, storage, and maintenance of metal equipment in corrosive environments reduces the risk of corrosion-related issues.
Combat Corrosion
Preventing corrosion caused by saltwater and freshwater requires a proactive approach. Understanding the causes, implementing preventive measures, conducting regular maintenance, and investing in education and training are vital steps. By embracing these strategies, we can combat corrosion effectively, extend the lifespan of metal assets, ensure safety, and enhance operational efficiency in both saltwater and freshwater environments. Together, we can defeat the ravages of corrosion and secure a brighter future for metal infrastructure.
Questions?
Our staff is always available to answer your questions.
Categories