Why Your Industrial Workspace Needs Thermal Spray Coatings
Thermal spray coating is a process where a spray of finely divided semi-molten and molten droplets deposits coatings of cermets, metals, polymers, and ceramics onto metallic and non-metallic surfaces. This process is beneficial because it allows for precision protection with high performance materials and can deposit coatings in layers ranging from 0.1mm to 1mm. Here are some reasons why your workspace needs thermal spray coatings:
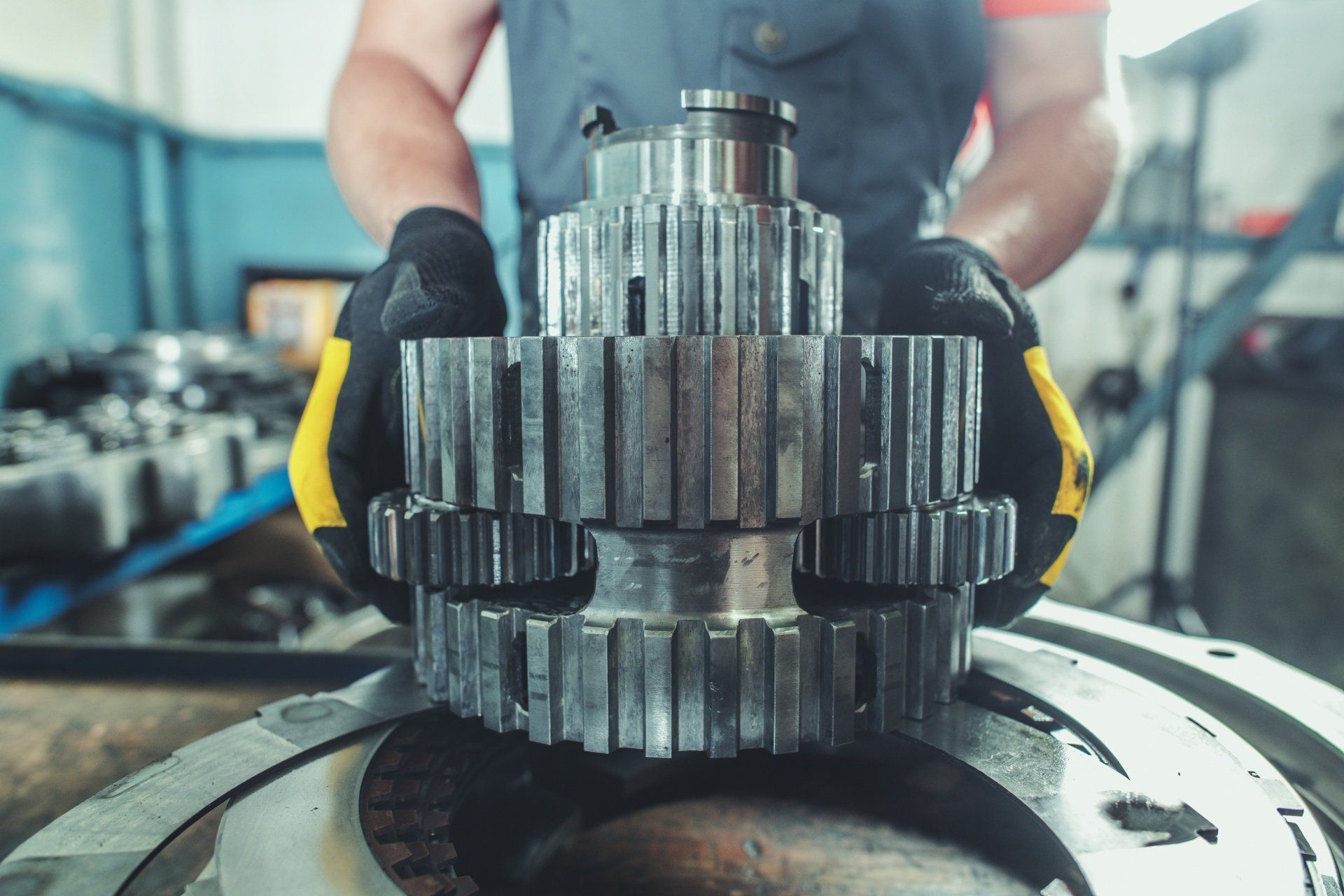
Fast and Effective Repair of Worn Metal Components:
Coatings applied by thermal spraying can quickly build up damaged or worn areas, where metal has been lost to vibration, wear, rubbing, or galling. These materials can restore dimension to get equipment back in operation quickly, with minimal distortion, and with like-new performance. Harder wearing materials can also be applied so that the repaired surface performs better and longer than the original equipment.
High-Performance Materials Where You Need Them
Thermal spray coatings are used to protect surfaces from corrosion or wear. Coatings can be applied to specific areas affected by surface attacks so that only the area that needs special protection is treated. This is more efficient than creating a full component from costlier materials for corrosion protection or wear resistance, or plating the entire component.
No More Need for Exotic Billets, Forgings, and Bars
Creating components from high performance alloys such as Inconel, Hastalloy, or bronze requires time, effort, and expense, often using custom castings or forgings. Thermal spray coatings make it possible to use the outstanding characteristics of these materials on components made from more accessible, and often more machinable materials.
Various Applications on Plastics and Most Metallic Substrates
Thermal spray coatings are not affected by metallurgical interactions with the substrate that would make some material pairings un-weldable. For example, aluminum can be applied to steel or tungsten carbide to copper without issue. Metallic coatings can even be applied to some plastics and carbon fiber reinforced plastic. There is a wide variety of coating metallic and ceramic materials available that can be applied to the target substrate. This yields great flexibility regarding what can be coated and how it can be used.
Wide Ranges of Wear and Corrosion Resistance
Thermal spraying can apply a broad spectrum of metallic and ceramic materials, each with unique thermal characteristics, hardness, resistance or interaction with chemicals and compounds, electrical resistivity and conductivity. Coatings can be tailored to meet the specific needs of an application; there is no one-size-fits-all solution. Whatever the particular needs of your project are, Hayden can help you select the right coating to improve your surface.
Layering of Materials for Tailored Performance
Thermal sprayed coatings are typically deposited at about 0.001” (0.025mm) per layer, and one layer of deposited material will not metallurgically interact with the layer beneath it. As such, multiple materials can be deposited sequentially to create overlays that change in composition or behavior through their cross section. Common examples include the addition of bond coats beneath some hard or rigid top coats, insulating layers beneath conducting layers to create sprayed-on heating elements, and materials of varying dielectric properties to create batteries and capacitors.
Formable Electrical Conductors and Insulators
Aluminum, copper, tungsten, and zinc are materials often used in electrical applications because they have low electrical resistance. This means they can easily conduct electricity and help protect surfaces from electrical damage or interference when applied as a gasket, shield, or barrier. Customized traces can also be applied onto surfaces such as antennas, equipment housings, and photovoltaic cells.
Some Coatings Are Effective Thermal Heat Barriers
Thermal spray coatings of some very high melting point ceramics can be sprayed onto metals to protect them from extreme temperatures. These coatings are effective at guarding against temperatures in hydrocarbon combustion, but have also been adapted for use in high performance automotive applications to mitigate heat transfer.
Minimal Impact on Substrates
Parts being coated by thermal spraying typically remain below 300 degrees Fahrenheit. Although the coating materials themselves sometimes have very high melting points, the coating process ensures that the target surface remains much cooler. There is often virtually no risk of distortion due to the application of a sprayed coating, and so finished parts with tight tolerances can be coated or repaired without jeopardizing fit.
Get Quality, Precision, and Flexible Thermal Spray Coatings from Hayden Corporation
At Hayden Corporation, we stake our reputation on long-standing thermal spray coating expertise. Our customers turn to us as their strategic thermal spray partner because of our focus on flexibility and quality, with handling capacities up to six tons, 72 inches in diameter, and 400 inches in length, along with customized
thermal spray coating applications for your components. To learn more, visit our website today!
Questions?
Our staff is always available to answer your questions.
Categories