The Power of Metallizing: Exploring the Advantages and Applications of Thermal Spraying
Metallizing, also known as thermal spraying or metal spraying, is a surface coating process that involves the application of metallic materials onto a substrate. It is a versatile technique used to enhance the properties of the surface, improve its performance, and provide protection against wear, corrosion, or other environmental factors.
During the metallizing process, a feedstock material, typically in the form of wire or powder, is heated to a molten or semi-molten state. The molten material is then propelled onto the substrate using compressed air or another suitable medium. Upon impact with the substrate, the material solidifies, forming a coating that adheres tightly to the surface.
Metallizing offers several advantages. It allows the deposition of a wide range of metals, alloys, and composites. It is suitable for various substrates, such as metal, plastic, concrete, or even fragile materials. It provides excellent bonding strength, creating a durable and long-lasting coating. Metallizing is used in numerous industries, including aerospace, automotive, marine, oil and gas, and heavy manufacturing to improve component performance, extend the lifespan of equipment, and protect against corrosion or wear.
Common Metallizing Materials
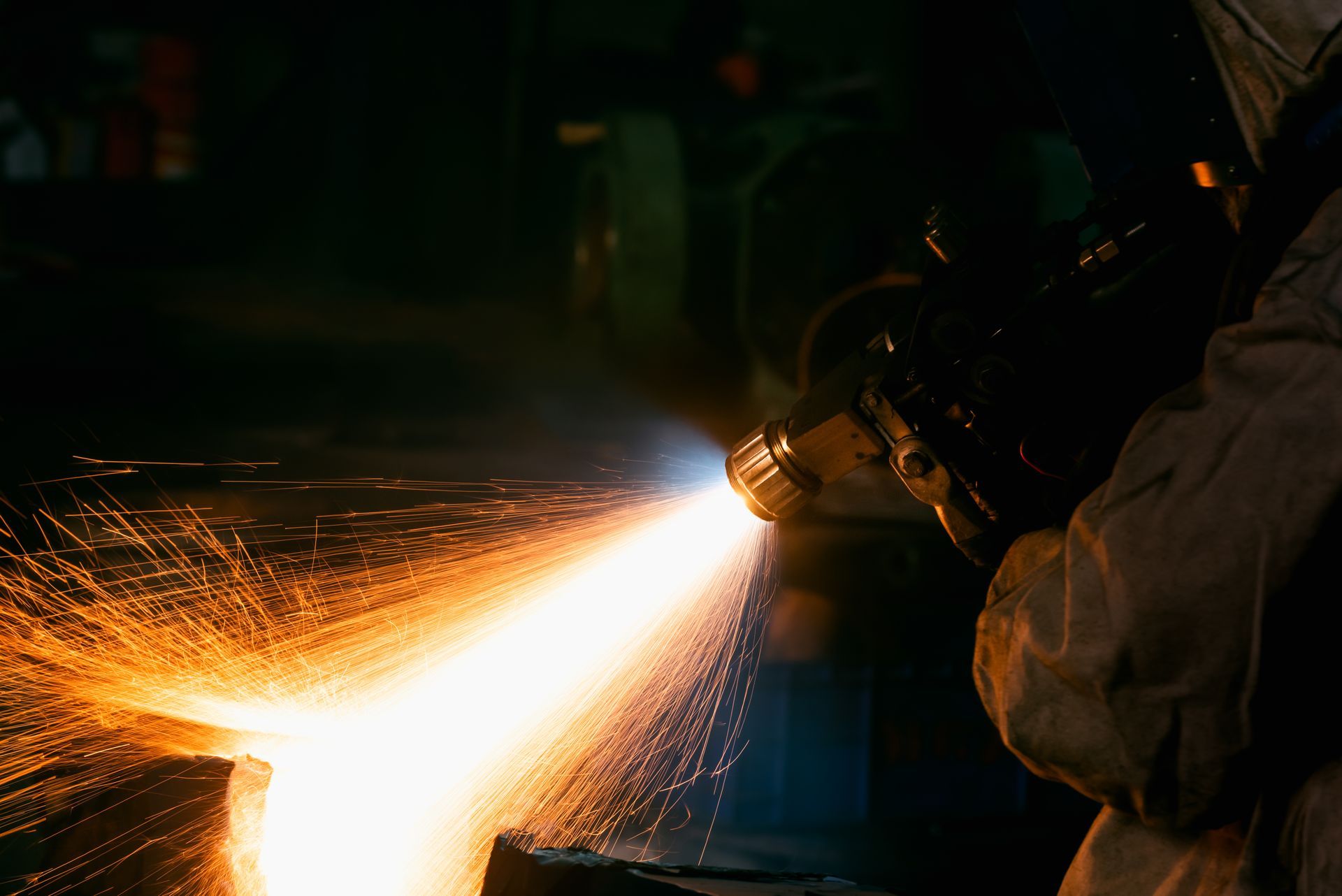
Metallizing can involve a variety of materials, including metals, alloys, and metallic composites. The choice of material depends on the specific application requirements and the properties desired for the coating. Here are some of the most common materials:
- Pure Metals: Metals such as aluminum, zinc, copper, and nickel are frequently used in metallizing. These materials offer excellent corrosion resistance, thermal conductivity, and electrical conductivity. Aluminum is particularly popular due to its light weight and high resistance to corrosion.
- Alloys: Alloy compositions can be customized to meet specific performance requirements. Common alloy materials used include stainless steel, bronze, and nickel- and cobalt-based alloys. These alloys offer a combination of strength, wear resistance, and corrosion resistance, making them suitable for a wide range of applications.
- Metallic Composites: Blends or other mixtures of hard materials such as tungsten carbide or chromium carbide with metallic binders like nickel and cobalt can also be sprayed by metallizing. These composite materials often have hardness and wear resistance well in excess of conventional metals and alloys.
It's important to note that the choice of metallizing material depends on factors such as the substrate, environmental conditions, desired properties, and intended application. Different materials offer unique characteristics and performance benefits, allowing for customization to meet specific needs.
Benefits of Metallizing
Metallizing, or thermal spraying, offers several benefits that make it a preferred surface coating technique in various industries. Here are some of the key advantages:
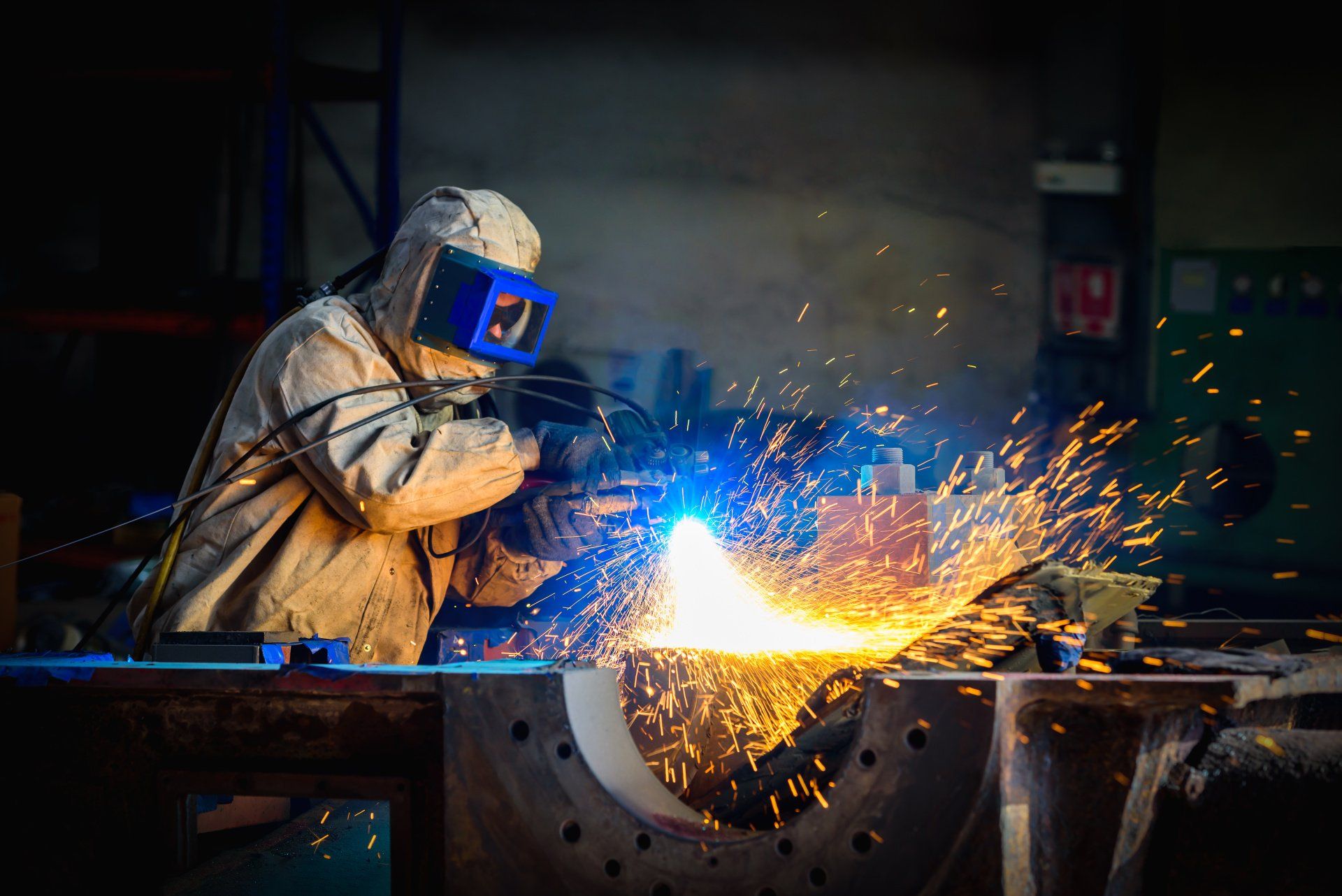
- Enhanced Protection: Metallizing provides effective protection against wear, corrosion, erosion, and other environmental factors. The deposited coating acts as a barrier between the substrate and the surrounding environment, preventing direct contact and minimizing damage to the underlying material. This protection extends the service life of components and equipment, reducing maintenance costs and downtime.
- Versatility in Material Selection: Metallizing allows for a wide range of material options, including metals, alloys, and composites. This versatility enables the selection of specific materials that possess desired properties such as hardness, wear resistance, thermal conductivity, electrical insulation, or chemical resistance. The ability to customize coatings based on the application requirements is a significant advantage.
- Compatibility with Various Substrates: Metallizing can be applied to different substrates, including metals, plastics, concrete, and composites. It ensures excellent adhesion and bonding strength between the coating and the substrate, regardless of the material's composition or surface characteristics. This versatility makes this process suitable for a wide range of industries and applications.
- Cost-Effectiveness: Coatings are often a cost-effective solution compared to alternatives such as welding, plating, or full-component replacement. The process minimizes material waste by utilizing a high percentage of the feedstock material, reducing material consumption and associated costs. Additionally, the protective coatings help extend the lifespan of components, reducing the frequency of replacements and maintenance requirements.
- Flexibility and Customization: Metallizing offers flexibility in terms of coating thickness, texture, and composition. The process allows for the deposition of coatings with varying thicknesses to meet specific application requirements. Coatings can be tailored to provide specific properties such as increased hardness, improved adhesion, or optimized thermal conductivity.
- Rapid Application and Minimal Downtime: Thermal spraying is a relatively quick process, enabling efficient application and minimal downtime. The coatings can be applied rapidly, and the coated components can often be put back into service soon after the process is completed. This efficiency is particularly beneficial for industries that require quick turnaround times and minimal interruption to operations.
Overall, the benefits of metallizing include enhanced protection, material versatility, compatibility with different substrates, cost-effectiveness, flexibility in customization, and efficient application. These advantages contribute to improved performance, extended component lifespan, reduced maintenance costs, and enhanced operational efficiency in various industries and
applications.
Questions?
Our staff is always available to answer your questions.
Categories