Unlocking the Potential: The Top Reasons to Use Arc Spray
When it comes to coating technologies, thermal arc spray stands out as a powerful and versatile method that offers a broad range of benefits. By employing an electric arc to generate high temperatures, this process enables the rapid deposition of durable coatings onto various surfaces. In this article, we will explore the top reasons why arc thermal spray has gained popularity across industries and why it is worth considering for your coating needs.
Major Uses of Arc Thermal Spray
Thermal spray technology has made significant progress over the years. It has evolved from spraying basic metals and simple alloys to now being able to spray extremely hard ceramics and carbides. However, these advancements do not diminish the value of arc spray. Different processes have specific applications in the coating world. Twin wire arc spray, for instance, is ideal for tasks such as dimensional restoration, sacrificial corrosion coatings, custom alloy coatings, and bearing surfaces.
- Dimensional Restoration
Arc thermal spray is a valuable technique employed for dimensional restoration, allowing the repair and rebuilding of worn or damaged components to their original dimensions. When a component experiences wear, erosion, or corrosion, its critical dimensions can be compromised, affecting its functionality and performance. Arc spray addresses this issue by depositing layers of molten particles onto the damaged surface, effectively restoring the dimensions and integrity of the component. By carefully controlling the deposition process, arc spray enables precise buildup of material, ensuring that the restored component aligns with its original specifications.
In this application, arc spraying has the advantage of being able to deposit material quickly and with good bond strength. Coatings for repair applied by arc spraying lock tightly to the surface because the applied material is fully melted prior to impact. Flexibility makes arc thermal spray a preferred choice in industries such as manufacturing, heavy machinery, and infrastructure, where downtime is at a premium. - Sacrificial Corrosion Coatings
Arc spray is widely utilized for sacrificial corrosion coatings, providing durable protection to metal substrates in corrosive environments. Sacrificial corrosion coatings use a more reactive metal that is applied as a protective layer over the substrate. When exposed to corrosive elements, the sacrificial metal corrodes instead of the underlying substrate, safeguarding it from damage.
Arc spray enables the deposition of sacrificial coatings by melting and projecting particles of the desired sacrificial metal onto the surface. Common sacrificial metals used include zinc, aluminum, and their alloys. These coatings create a barrier that shields the substrate, ensuring that any corrosion occurs primarily on the sacrificial layer.
Arc spraying has the capability to cover substantial surface area quickly, which makes it well suited to large scale corrosion protection work, as with structural steel, bridges, outdoor piping, etc. This application is extensively employed in marine environments, infrastructure exposed to harsh weather conditions, and industrial facilities where corrosive agents are present, effectively extending the service life of coated structures and components. - Custom Alloy Coatings
Arc spray offers a unique method for creating custom alloy coatings, offering tailored solutions to meet specific performance requirements. Since the arc is created between two oppositely charged consumable wires, and the wires are fully melted during spraying, two wires of differing composition can be used to create a coating which is essentially an alloy of the two primary materials.
With arc thermal spray, different alloy compositions can be precisely deposited onto substrates, allowing the formation of coatings with unique properties and characteristics. By carefully selecting the appropriate alloy materials and adjusting the spray parameters, desired attributes such as enhanced strength, wear resistance, or specific thermal properties can be achieved.
Virtually any metallic material that can be drawn into conventional 1/16” wire is useable in this process, facilitating the customization of coatings to suit the specific needs of various industries, including aerospace, automotive, and manufacturing. Whether it's a specialized alloy for high-temperature applications or a unique combination of metals for improved corrosion resistance, arc thermal spray enables the creation of custom alloy coatings that deliver optimal performance and functionality in diverse operating conditions.
Advantages of Arc Spray
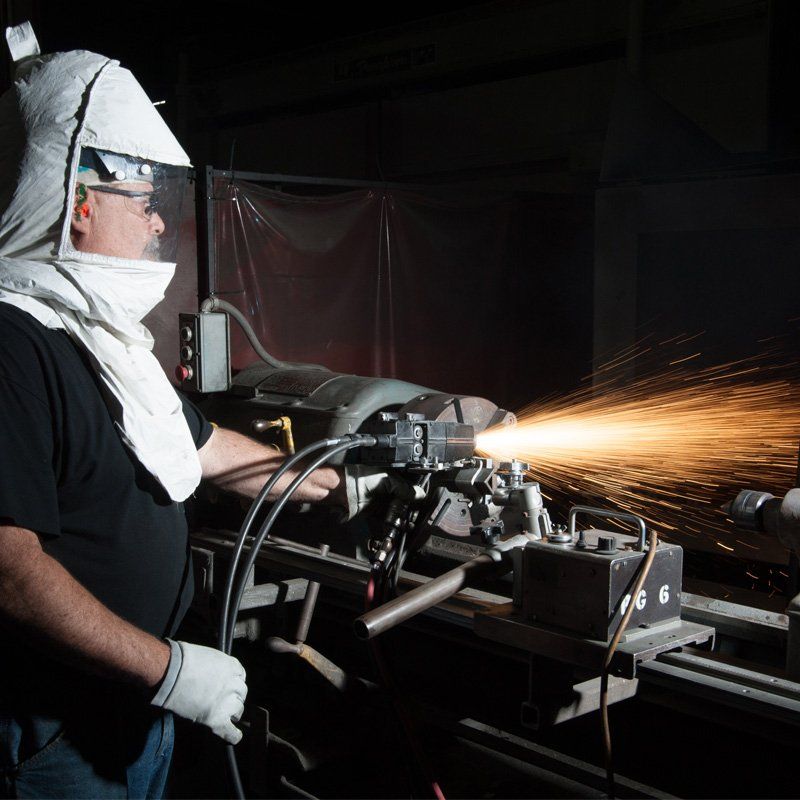
- Enhanced Coating Durability
Arc spray creates coatings with exceptional durability. By fully melting the feedstock wires before deposition, this process forms coatings that exhibit remarkable resistance to wear, corrosion, and erosion. Industries such as aerospace and automotive rely on these robust coatings to protect critical components from harsh environments and extend their lifespan significantly. - Versatility in Material Selection
One of the key advantages of arc spray is its versatility in material selection. This process can utilize a wide range of metals, allowing for tailored coatings that suit specific applications. From high-strength alloys to oxidation-resistant corrosion protection to non-galling bearing materials, arc thermal spray opens doors to diverse material options that can meet the requirements of different industries and unique coating challenges. - Cost-Effectiveness
In addition to its performance benefits, this process is uniquely cost-effective. Due to its simplicity, minimal process requirements, and high deposition rate, arc spraying is often the least expensive thermal spray technology to implement. It minimizes material waste through its high deposition efficiency, reducing overall material consumption. Moreover, the durability and longevity of these coatings translate into significant cost savings over time due to reduced maintenance and reapplication needs. - Improved Surface Restoration:
Arc spray excels at surface restoration, making it an ideal choice for repairing worn or damaged components. By depositing new layers onto degraded surfaces, this process rejuvenates and reinforces the substrates, effectively extending their service life. Industries relying on heavy machinery or industrial equipment can greatly benefit from this coatings ability to restore surfaces, mitigating the need for costly replacements and minimizing downtime. - Enhanced Performance and Functionality:
Beyond surface protection and restoration, arc thermal spray can significantly enhance the performance and functionality of coated components. With precise material selection and control over coating thickness, this process can impart desired characteristics such as heat resistance, electrical conductivity, or insulation properties. Industries such as power generation and oil and gas leverage these improvements to optimize equipment performance and ensure operational efficiency in challenging environments. - Environmental Advantages:
Twin wire arc spray also offers environmental advantages over traditional coating methods. The process generates minimal waste, as it maximizes material utilization and reduces the need for hazardous substances. This aligns with the growing emphasis on sustainability and responsible manufacturing practices. By opting for arc thermal spray, industries can minimize waste generation, lower their environmental footprint, and comply with stringent regulatory standards.
Conclusion:
Arc spray has emerged as a reliable and versatile coating method, offering numerous advantages across various industries. With its enhanced coating durability, versatility in material selection, cost-effectiveness, surface restoration capabilities, improved performance, and environmental benefits, it has become a go-to choice for coating needs. As technology advances further, we can expect even greater potential and advancements in the field of arc thermal spray, unlocking new possibilities for industries seeking reliable and efficient coating solutions.
Questions?
Our staff is always available to answer your questions.
Categories