Understanding Thermal Barrier Coatings
Thermal barrier coatings (TBC) are thick coatings of very high melting point and low-heat-transmission material applied to metal components to protect them from thermal damage. They are commonly used in industrial and commercial applications, such as gas turbines, jet engines, and industrial furnaces. TBCs typically consist of a ceramic top layer that is bonded to the metal substrate with a metallic bond coat. The TBC layer's thickness is generally in the range of 500-1000 microns. The primary function of the TBC is to reflect heat away from the metal substrate, thus preventing it from reaching temperatures that would cause thermal damage. In addition, TBCs can also help improve the overall efficiency of industrial equipment by reducing heat losses.
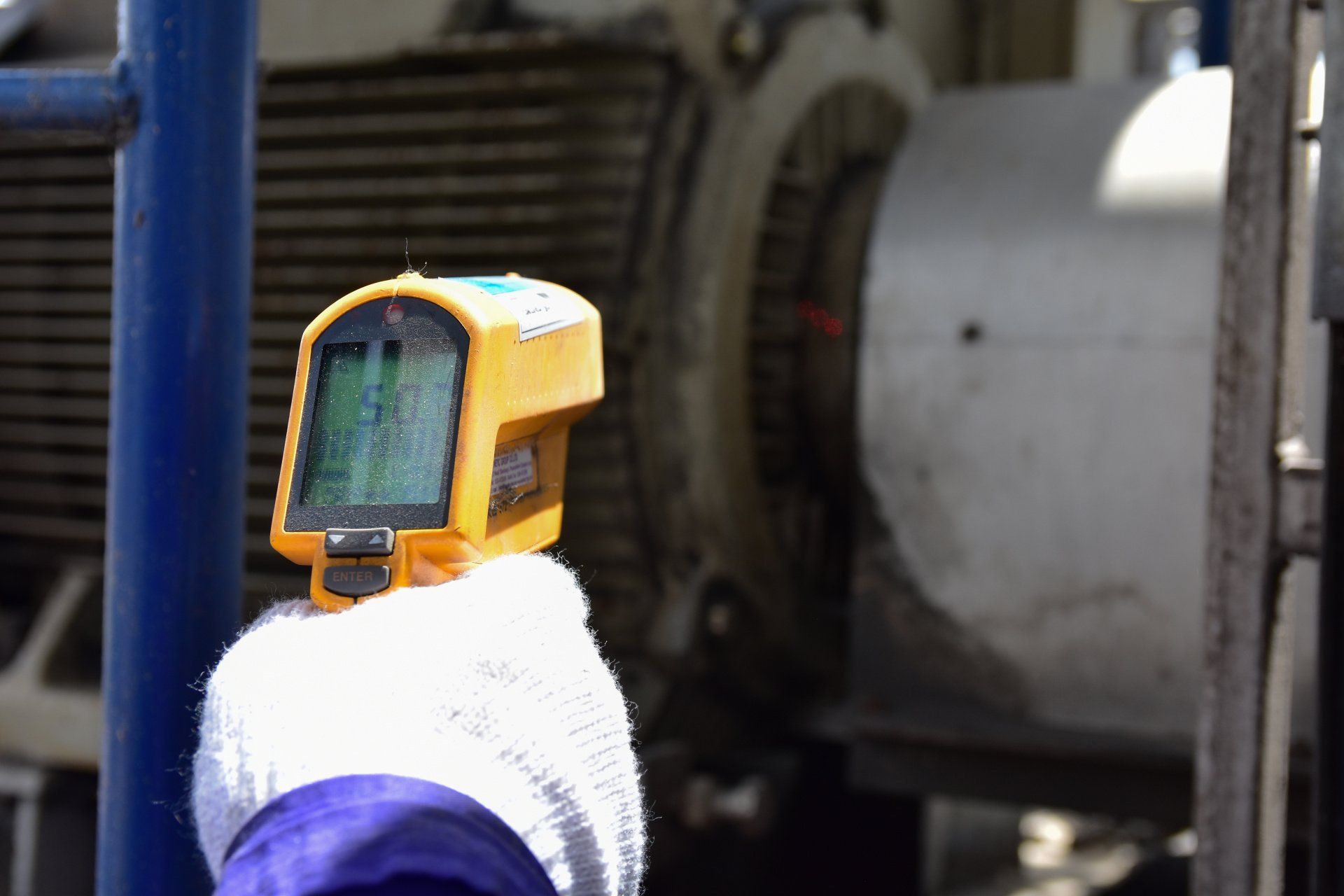
How are Thermal Barrier Coatings Applied?
Thermal barrier coatings are commonly applied using a thermal spray process. In this process, the TBC coating is atomized into microscopic particles and then sprayed onto the metal substrate. The particles impact, cool, and become bonded to the surface of the substrate. Various thermal spray processes can be used, including plasma spraying and high-velocity oxygen fuel spraying (HVOF).
Applications Include:
- Turbine blades
- Exhaust nozzles
- Combustion chambers
- Piston rings
What are the main benefits of Thermal Barrier Coatings?
Thermal Barrier Coatings offer several benefits, including:
- Protecting metal components from thermal damage
- Improving the efficiency of industrial equipment
- Reducing heat losses
- Increasing the service life of components
- Withstands high temperatures and thermal cycling better than uncoated metals.
These benefits make thermal barrier coatings essential to many industrial and commercial applications.
What industries use thermal barrier coatings most frequently?
Thermal barrier coatings can be found in a variety of industries, including:
Aerospace
TBCs are used to protect engine components from the high temperatures generated during combustion of fuel in the engines. TBCs can also be used to improve the efficiency of gas turbines by reducing heat loss through the engine's walls.
Power generation
In the power generation industry, TBCs are often used on turbine blades and other hot section components to prolong their lifespan and prevent damage from overheating. The most common types of TBCs are made from yttria-stabilized zirconia (YSZ), which is a highly durable material that can withstand temperatures of up to 3000 degrees Fahrenheit. In addition to protecting turbine blades from damage, TBCs can also improve the efficiency of power plants by keeping heat inside the combustion chamber, where it can be used to generate electricity. As the demand for cleaner and more efficient power generation increases, thermal barrier coatings will likely play an increasingly important role.
Automotive
Thermal barrier coatings are also used in the automotive industry to protect engine components from the high temperatures generated by internal combustion. TBCs can be used on various engine parts, including piston rings, exhaust valves, and turbocharger housings. In addition to thermal protection, TBCs can also improve the efficiency of engines by reducing heat losses.
Protect Your Metal Components
Thermal barrier coatings are an essential part of many industrial and commercial applications. If you are looking for a way to protect your metal components from thermal damage, or improve the efficiency of your equipment, then thermal barrier coatings may be the right solution for you.
If you have any questions about thermal barrier coatings or how they can be utilized in your application, please
contact Hayden Corp. We would be happy to discuss your specific needs and requirements.
Questions?
Our staff is always available to answer your questions.
Categories